Ever wondered how the tiny optical lenses in your devices are made with such precision? It’s all thanks to the THY Precision Injection Molding Optical Lenses process step by step. THY Precision leads in making top-notch optical lenses using this tech.
Nowadays, Injection Molding Optical Lenses process step by step is key in making optical parts like Fresnel lenses and aspheric lenses. This method lets us make lots of these parts quickly and with great precision. It’s super useful for many industries, from cars to medical devices.
Key Takeaways
- Injection Molding Optical Lenses has changed how we make optical parts, making it fast and precise.
- Optical plastics in Injection Molding Optical Lenses process step by step can mimic glass in complexity and optical quality.
- This process can create complex shapes and tiny details, ensuring every piece is the same.
- THY Precision uses Injection Molding Optical Lenses process step by step to make advanced optical lenses.
- Its mix of precision, speed, and cost makes injection molded optical lenses a big deal across industries.
Introduction to Injection Molding Optical Lenses
The world is moving fast towards optical technology, making the need for high-quality optical parts more pressing than ever. At THY Precision, we know how crucial precision and efficiency are in the Injection Molding Optical Lenses process step by step for making optical lenses. Optical polymers are now a top choice over glass because they’re tough, affordable, and light, which boosts the performance of optical parts.
The plastic Injection Molding Optical Lenses method is key for making polymer parts because it’s fast, can create complex shapes, and ensures accuracy. The injection moulding cycle has five main steps: mould clamping, polymer injection, packing pressure, cooling, and part ejection.
For top-notch quality, the design of the injection mould and the injection unit are vital in plasticizing and melt delivery. At THY Precision, we’ve honed these skills to give our clients unmatched optical parts that meet strict standards.
As technology advances, THY Precision leads in product quality control for injection-molded optical lenses. Our drive for innovation and excellence means our clients get the best solutions for their optical needs.
“Precision and efficiency are the hallmarks of our injection molding process for optical lenses.”
Injection Molding Optical Lenses – Optical Polymer Materials and Properties
Choosing the right injection moulding process step by step is key for making top-notch optical lenses. The top picks for plastic injection moulding are Poly(methyl methacrylate) (PMMA), polycarbonate (PC), cyclic olefin copolymer (COC), and cyclic olefin polymer (COP). These materials are great because they don’t stress easily, absorb little water, and stand up well to the weather. They’re perfect for injection mould design and injection moulding cycle.
Common Optical Polymers
- Poly(methyl methacrylate) (PMMA): This material is versatile, clear, strong, and can handle the weather well. It’s a top pick for many optical uses.
- Polycarbonate (PC): PC is super tough, clear, and light, making it great for making optical lenses and parts.
- Cyclic Olefin Copolymer (COC): COC is clear, has low birefringence, and doesn’t absorb much water. It’s perfect for precise optical tasks.
- Cyclic Olefin Polymer (COP): Like COC, COP is clear, dry, and stays the same size. It’s great for high-quality optical jobs.
Optical and Mechanical Properties
Picking the right optical polymer for injection moulding cycle and injection mould design is vital. These materials have special optical and mechanical traits that affect how well the final part works. Things like mould clamping, injection unit, plasticizing, melt delivery, part ejection, and product quality control matter a lot. They help make sure the lens has the right look and feel.
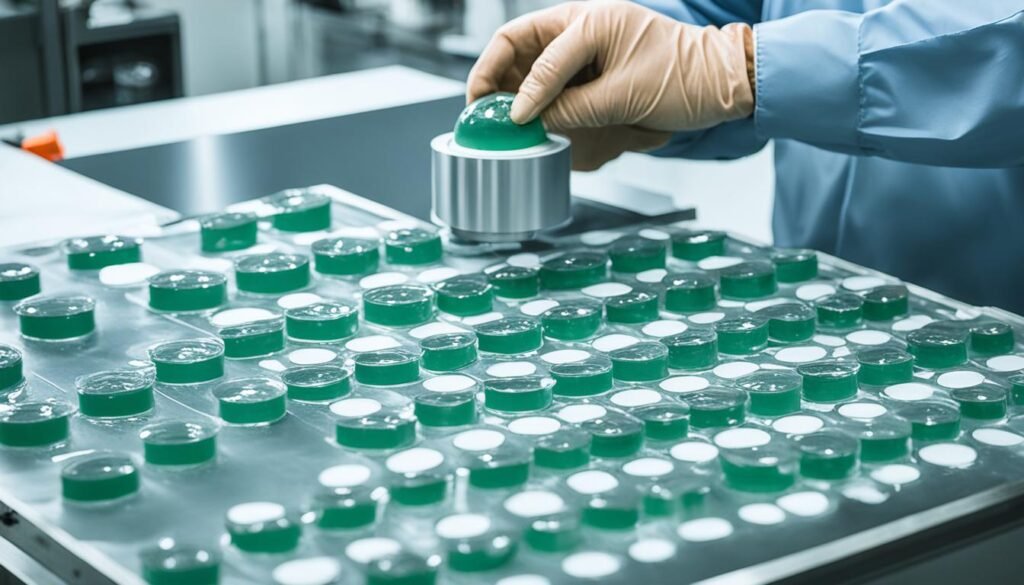
“The choice of optical polymer material is a critical decision in the plastic injection moulding of high-performance lenses, as it directly impacts the final product quality and performance.”
Injection Molding Process for Optical Lenses
The process of making optical lenses through injection moulding is complex and precise. At THY Precision, we excel in this method, creating top-notch optical parts that meet strict standards.
First, the mould for injection moulding is designed with great care. It sets the lens’s shape and specs. Choosing the right plastic is key, as it affects the lens’s optical and mechanical properties.
- Mould Clamping: The mould is clamped tightly, getting ready for the plastic.
- Injection Unit: The unit heats and mixes the plastic, preparing it for the mould.
- Plasticizing: The plastic is melted and mixed well in the unit for a consistent quality.
- Melt Delivery: The plastic is pushed into the mould, taking the shape of the lens.
- Cooling: The temperature is controlled during cooling, helping the lens solidify evenly without defects.
- Part Ejection: The finished lens is carefully taken out of the mould, keeping its quality and shape.
Quality checks are strict throughout the process to ensure the lenses are top-notch. From picking the material to ejecting the lens, every step is watched and fine-tuned. This ensures the lenses we deliver are of the highest quality, as our customers expect from THY Precision.
Process Step | Description |
---|---|
Mould Clamping | The injection mould is securely clamped, preparing it to receive the molten plastic material. |
Injection Unit | The injection unit heats and plasticizes the plastic resin, ready for delivery into the mould cavity. |
Plasticizing | The plastic material is melted and homogenized within the injection unit, ensuring a consistent melt quality. |
Melt Delivery | The molten plastic is then forcefully injected into the mould cavity, where it takes on the precise shape of the lens design. |
Cooling | Precise temperature control is maintained during the cooling process, allowing the lens to solidify gradually and uniformly, preventing defects such as warping or bubbles. |
Part Ejection | Finally, the fully formed optical lens is delicately ejected from the mould, preserving its optical properties and structural integrity. |
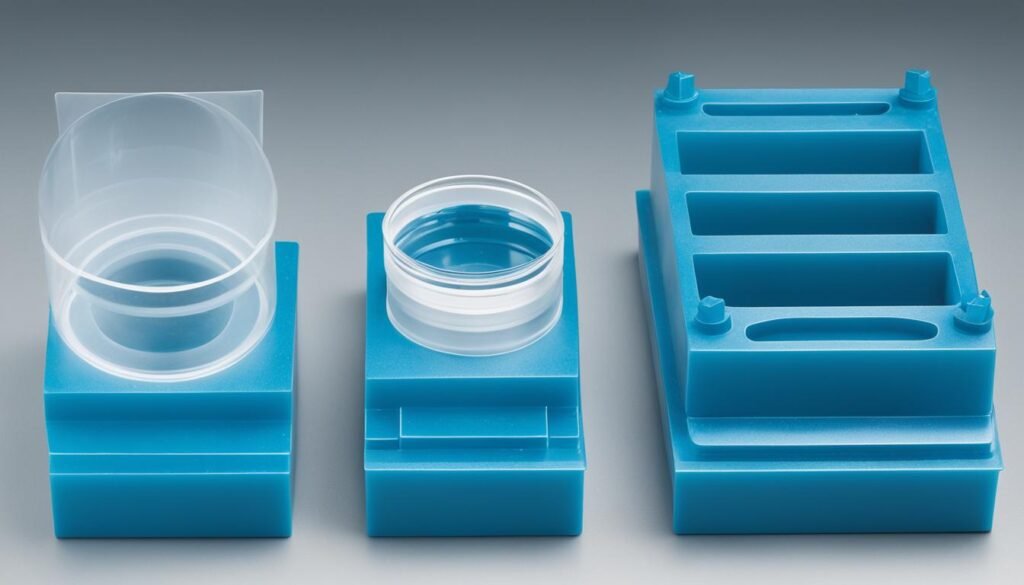
“At THY Precision, we are committed to delivering optical lenses of the highest quality through our expertise in the injection moulding process.”
Challenges and Solutions in Injection Molding Optics
Making high-quality injection moulded optical lenses is tricky. The process can cause stress and birefringence, which hurt the lens’s performance. These issues come from the way the plastic flows and cools during moulding.
THY Precision has found new ways to fix these problems. They use variotherm systems for quick heating and cooling of the mould. This helps reduce stress from temperature changes. They also try vacuum-assisted microinjection moulding to make the lenses more accurate and stress-free.
Another method they use is conformal cooling channels in the mould design. These channels help cool the plastic evenly, cutting down on stress. By tackling these issues, THY Precision makes sure their lenses are top-notch.
THY Precision works hard to overcome the challenges of moulding optical lenses. Their focus on innovation and quality control means their products meet high standards. This ensures their customers get the best optical lenses available.